Reliable Chinese Soup Maker Manufacturer
A Leading Chinese Manufacturer of High-Quality Electric Appliances
Founded in 2010, Foshan Shunde Wintrend Electric Appliances Industry Co., Ltd. is a Chinese soup maker manufacturer dedicated to researching, developing, producing, and selling high-quality household appliances. We are committed to providing customers with superior kitchen appliances, especially our renowned electric soup makers.
Advanced Technology and Uncompromising Quality
Equipped with state-of-the-art production facilities and a highly experienced R&D team, we offer efficient OEM/ODM services tailored to our clients’ specific needs. To ensure product excellence, Wintrend has achieved ISO9001:2015 quality management system certification and passed the BSCI social audit. Our products have obtained multiple international safety and environmental certifications including GS, CE, EMC, CB, SAA, and RoHS, and are widely sold in Europe, the Middle East, Australia, South America, and other regions.
READ MORE aobut WintrendHot Sale Products of Wintrend
Types of Electric Appliances We Made
OEM Chinese Soup Maker Manufacturer
Wintrend offer a range of OEM/ODM services, from product design and development to manufacturing and assembly.By partnering with Wintrend OEM electric appliances manufacturer, you can bring your innovative products to market efficiently and effectively.
Get A free quoteChinese Soup Maker Manufacturing Process
The manufacturing process for electric appliances such as soup makers involves a complex series of steps, from design and prototyping to assembly and quality control. Here’s a breakdown of the key stages:
1. Product Design and Development
- Concept Generation: Brainstorming and ideation of new appliance concepts.
- Market Research: Analyzing consumer trends and preferences.
- Design and Prototyping: Creating initial designs, prototypes, and testing.
- Specifications Development: Defining technical requirements and performance standards.
2. Component Sourcing and Procurement
- Supplier Selection: Identifying and evaluating suppliers for components and materials.
- Purchasing: Placing orders and managing inventory.
- Quality Control: Ensuring components meet specifications and quality standards.
3. Assembly and Testing
- Assembly Line: Assembling components into the final product.
- Functional Testing: Verifying that the appliance operates as intended.
- Quality Control: Inspecting for defects and ensuring compliance with standards.
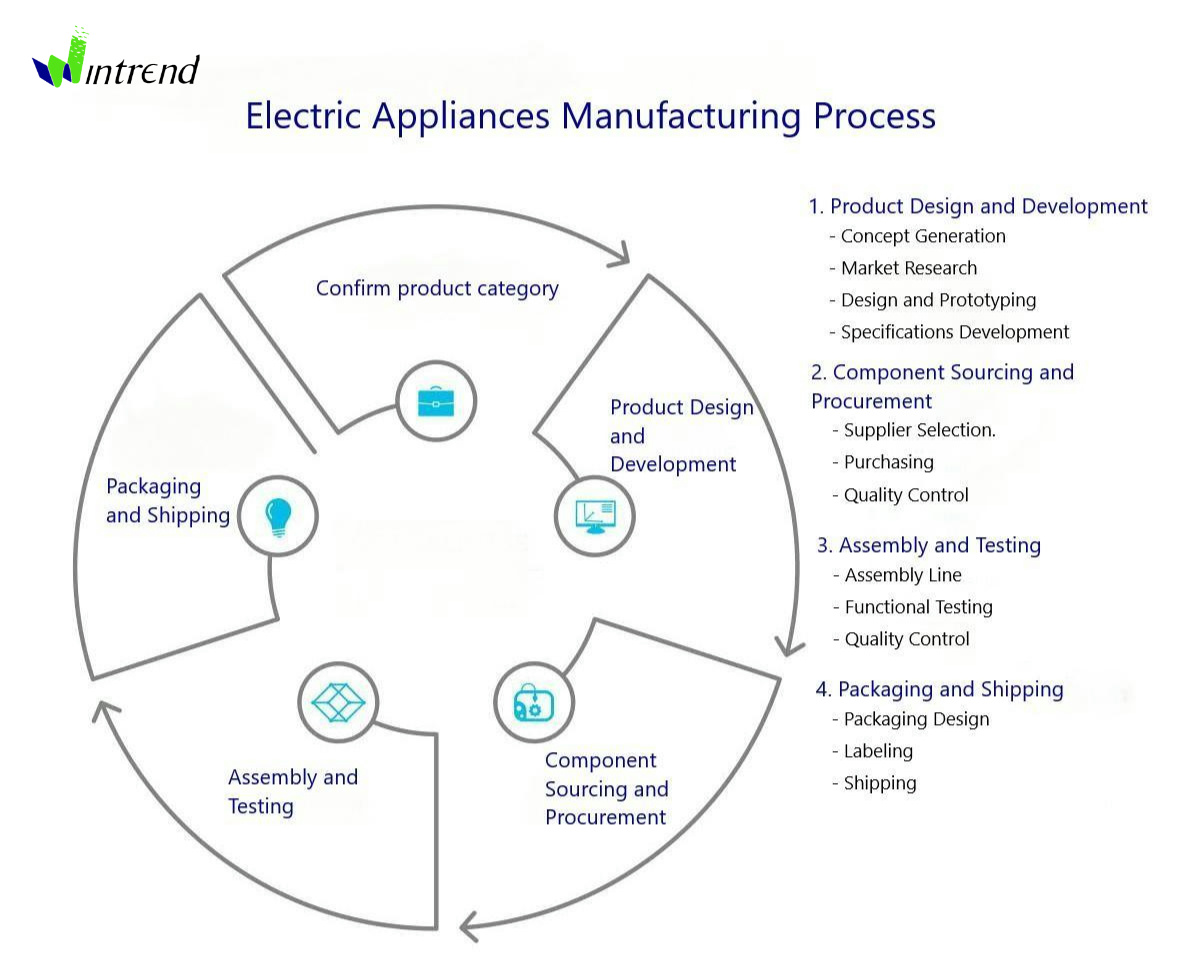
4. Packaging and Shipping
- Packaging Design: Creating appropriate packaging for shipping and retail display.
- Labeling: Applying labels with product information, barcodes, and certifications.
- Shipping: Coordinating logistics and transportation to distribution centers or retailers.
Why Choose Us as Chinese Soup Maker Supplier
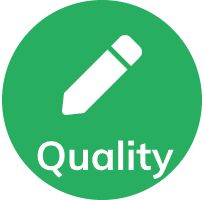
Quality and Reliability
Wintred uses only the best materials to ensure durability. Our Chinese soup makers incorporate cutting-edge features for optimal performance. And all products are under strict quality control.
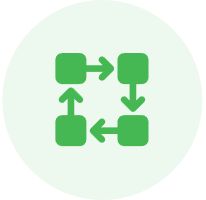
Customization Options
Wintrend customizes Chinese soup makers to match your specific requirements. We choose from a variety of options to create the perfect product and produce products under your brand name.
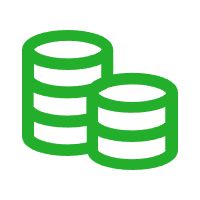
Competitive Pricing
We offer competitive pricing without compromising quality. Customers enjoy significant savings on large orders. Besides, we can accommodate your specific payment preferences.
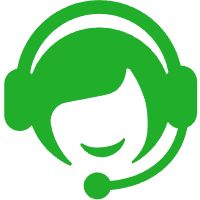
Excellent Service
Wintrend team is always available to assist with your inquiries. We ensure timely delivery of your orders as discussed and customers can have comprehensive support and warranty coverage.
What Our Customers Say About Chinese Soup Makers
After-Sales Support of Chinese Soup Makers
1. Prompt Response
Establish dedicated customer support channels, such as phone lines, email, and online chat.Train customer support staff to handle inquiries and complaints effectively and efficiently.Implement a system to track and prioritize customer issues to ensure timely resolution.Set clear response time targets and strive to meet or exceed them.
2. Technical Expertise
Hire or train technical support staff with in-depth knowledge of your products and their components.Provide ongoing training to keep staff updated on new product features and troubleshooting techniques.Equip support staff with diagnostic tools and resources to identify and resolve issues quickly.Encourage a culture of continuous learning and professional development.
3. Spare Parts Availability
Maintain a comprehensive inventory of spare parts to minimize downtime in case of repairs or replacements.Implement a system for tracking and managing spare parts inventory.Establish relationships with reliable suppliers to ensure timely procurement of parts.Consider offering extended warranty options or repair contracts for added peace of mind.
4. Warranty Management
Clearly communicate warranty terms and conditions to customers.Establish a streamlined process for warranty claims and repairs.Track and analyze warranty data to identify common issues and improve product quality.Offer extended warranty options to enhance customer satisfaction and loyalty.
5. Customer Feedback
Actively seek customer feedback through surveys, reviews, and social media.Analyze customer feedback to identify areas for improvement.Implement changes based on customer feedback to enhance product quality and service.Demonstrate a commitment to customer satisfaction by addressing concerns promptly and effectively.
Our Partner
FAQs About OEM Electric Appliances Manufacturing
The OEM manufacturing process for electric appliances typically involves:
- Product design and development: Creating the appliance concept, specifications, and prototypes.
- Component sourcing: Procuring necessary components and materials.
- Manufacturing: Assembling the appliance according to design specifications.
- Quality control: Ensuring the appliance meets quality standards and regulations.
- Packaging and shipping: Preparing the appliance for delivery to the client.
Partnering with an OEM manufacturer can offer several benefits, including:
- Cost-effective production: OEMs often have economies of scale that can lead to lower costs.
- Expertise: Access to specialized knowledge and experience in appliance manufacturing.
- Flexibility: Ability to customize products to meet specific needs.
- Time-to-market: Streamlined production processes can reduce time-to-market.
- Quality assurance: OEMs typically have quality control measures in place to ensure product reliability.
To ensure the quality of OEM-manufactured appliances:
- Conduct thorough due diligence: Research potential manufacturers and assess their reputation and capabilities.
- Visit their facilities: Inspect their production facilities and quality control processes.
- Request samples: Obtain samples of their products for testing and evaluation.
- Specify quality standards: Clearly communicate your quality requirements and expectations.
- Require certifications: Insist on relevant certifications, such as ISO 9001, to demonstrate quality commitment.
Lead times can vary depending on factors like product complexity, order quantity, and the manufacturer’s capacity. However, experienced OEM manufacturers can often provide estimates and work to meet your deadlines.
To protect your intellectual property:
- Non-disclosure agreements: Require confidentiality agreements from the OEM.
- Intellectual property rights: Clearly define ownership of designs, patents, and trademarks.
- Regular communication: Maintain open communication and oversight throughout the manufacturing process.
Common challenges include:
- Communication barriers: Language and cultural differences can sometimes hinder communication.
- Supply chain disruptions: Global events or economic factors can affect component availability and pricing.
- Quality control issues: Ensuring consistent quality can be challenging, especially in large-scale production.
- Intellectual property theft: Protecting your designs and innovations is crucial.